Effect of Mill undertollerance on Shell thickness calculation
Unfortunately, ASME VIII Div.1 doesn’t give a clear picture, whether to add the undertollerance in the min. required thickness as calculated by ASME VIII Div.1
ASME VIII Div. 2, give a clear cut understanding on this issue, can clears all ambiguity. (Clause 4.1.3)
The explanation goes as under
Mill Under tolerance. Plate material shall be ordered not thinner than the minimum required thickness.Vessels made of plate furnished with an under tolerance of not more than the smaller value of 0.3 mm (0.01 in.) or 6% of
the ordered thickness may be used at the full maximum allowable working pressure for the thickness ordered. If the specification to which the plate is ordered allows a greater under tolerance, the ordered thickness of the materials shall be sufficiently greater than the design thickness so that the thickness of the material furnished is not more than the smaller of 0.3 mm (0.01 in.) or 6% under the design thickness.
{The underline sentence is very clear, if they are in this limit, no need to add the allowance in calculation, which as per II-A, need to be part of purchase specification, and purchaser has to bid by it}
Pipe Under tolerance. If pipe or tube is ordered by its nominal wall thickness, the manufacturing under tolerance on wall thickness shall be taken into account. After the minimum wall thickness is determined, it shall be iincreased by an amount sufficient to provide the manufacturing under tolerance allowed in the pipe or tube specification.
{Again, this is very clear, we need to take this in account in our calculation}
So, Bottom line
If the shell is made from Plate (Rolled) and if purchase specs for Plate as per ASME II-A, then the vendor is binded to supply material within these limits, and we need not to consider additional allowance. But if your shell is made from Pipe, then you need to consider the 12.5% tolerance during calculation of thickness!
Hope this will help.
Earthquake loading – Brief
All designers are accustomed to evaluating moments due to eccentric and wind loads, but there are a few who may not be familiar with the method used for estimating moments due to earthquake. Therefore, the following brief outline is presented because this method is recommended as a design procedure for vessels where dynamic considerations are required. The weight of each vessel element (shell, head, tray, or internal part) is calculated. and then multiplied by the vertical distance from the circumferential seam (or horizontal plane) under
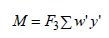
consideration to the center of gravity of the element. The summation of the moments so found ismultiplied by the seismic factor for the area where the vessel is to operate, thereby yielding a moment due to earthquake or seismic disturbance. For vessels, the seismic factor will usually have a value of 0.03 to 0.12, depending upon the geographical location. Expressed mathematically,
Share this:
Like this: